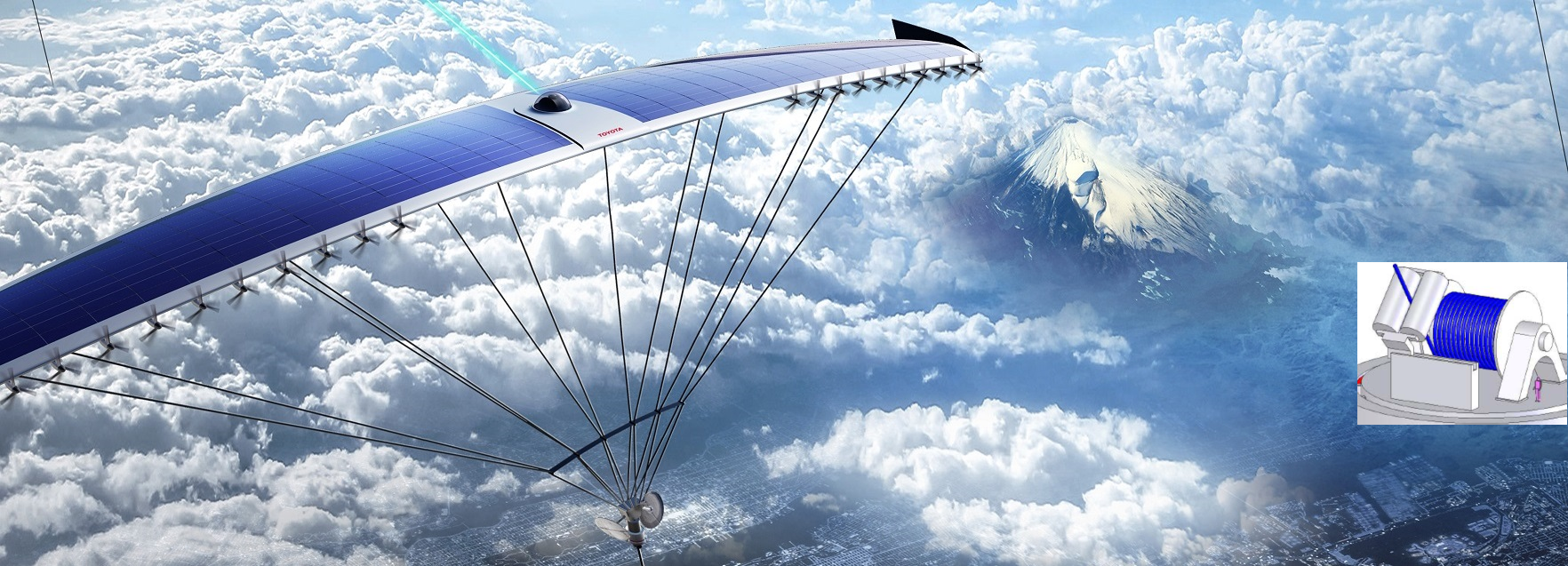
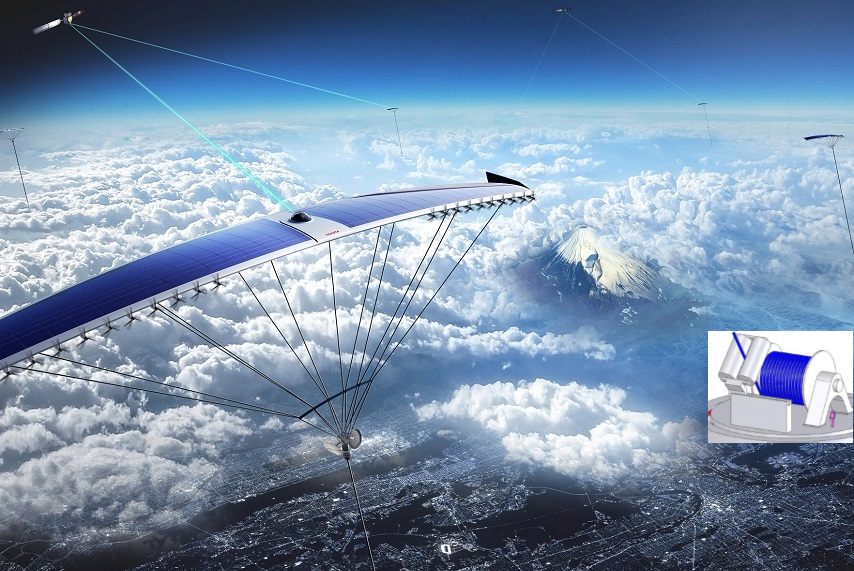
2022年1月21日
新エネルギー源を目指す「マザーシッププロジェクト」
―佐吉が愛した凧をヒントに。繊維産業が将来の空中プラットフォーム実現に貢献―
トヨタ自動車には豊田佐吉遺訓をまとめた豊田綱領があり、その中に「研究と創造に心を致し 常に時流に先んずべし」という言葉があります。私たち未来創生センターでは、将来日本が抱えるであろう社会課題を想定し、資源の多くを輸入に頼っているわが国の将来のエネルギーセキュリティのために2018年「マザーシッププロジェクト」※1※2を立ち上げました。「マザーシッププロジェクト」とはカイト(凧)を対流圏界面域に飛ばし、偏西風を利用し発電しようという研究です。この研究を実現させようとすると、例えば大きくて軽いカイトを作らなければならない、カイトをテザー(凧糸)で滞空させなければならない、など多くの課題があります。今回は「マザーシッププロジェクト」の中でも、オンリーワン技術が詰まったカイトの「基材」について紹介いたします。
プロジェクト概要
カーボンニュートラルの観点から再生可能エネルギーを活用することが求められています。いくつかの再生エネルギー源がある中でも世界の中で最も平均風速の高いと言われている、日本上空域の偏西風に着目しました(図1)。「マザーシッププロジェクト」では、上空約10㎞の偏西風域で大きなカイトを揚げ、そのカイトは高強度のスーパー繊維(高い強度と弾性率を持つ繊維)のテザー(凧糸)で地上にある発電機に係留し、そこで「発電」させます(図2左図)。また図2右図のように、隣接するカイトをワイヤーでつなぎ、地上から持ち上げた荷物をカイトの間で移動する運搬「スカイフック」や、高空を活かした衛星光通信の地上への「雲上中継地」など滞空性プラットフォームとしての活用を想定しています。
-
図1 上空10km付近の10年間平均風速分布(引用元:NOAA/ESRL Physical Sciences Division, Boulder Colorado)
-
図2 「マザーシッププロジェクト」全体概要
社内自発テーマとして研究開発開始、でも苦戦の連続
「マザーシッププロジェクト」は2018年に5名で開始しました。このプラットフォームを成立させるための大事な技術要件のひとつに、いかにカイトの部分を軽量に実現できるかがあります。カイトであることから、航空機のような剛体構造ではなく軽量で柔軟性に優れたほうがよいため、我々は「膜体インフレータブル構造」を選択しました。膜体インフレータブル構造とは、軽くて強い布で出来た筒状(インフレータブルチューブ)の外皮を骨格とし、筒の中の空気の内圧を内皮という自転車タイヤのチューブのような袋で保持しその剛性を保たせる構造です(図3)。自ら設計、製作、評価技術を習得するため、まず7m²程度の小型カイトを試作から着手しました。外皮の基材は、スーパー繊維を積層し樹脂で含浸しシート状に硬化した複合材料(図4)を購入し、試行錯誤で開発を進めました。
-
図3 開発した小型カイト。膜体インフレータブル構造を採用
-
図4 従来基材。基材は繊維積層構成(同方向に並べたスーパー繊維の層を直交させ積層し、樹脂で含浸し硬化させた複合材料)
飛行試験は非常に苦戦しましたが、航空工学、材料力学、制御工学などを駆使し2020年5月に最初の目標である地上高度1,000m飛行を達成しました(動画1)。飛行試験については後日、別のレポートで報告します。
-
動画1 地上高度1,000m到達(画像の上にカーソルを置くと、動画が自動再生されます)
新基材開発の決意
数回の飛行試験により、カイトの滞空性能を上げるためには、カイトをより軽く、強風に対する耐荷重性の高く、かつ、縫い目部分に滑脱(縫い目周りの繊維の間が開く現象、図5参照)が起きにくい基材で作らないといけないという結論に至りました。小型カイトで使っていた従来基材は、図4のように繊維層の密度にばらつきがあったため狙った耐荷重をクリアしていませんでした。また縫い目部分に高い荷重がかかると滑脱が発生し、結果カイトの骨格が脆くなるという問題点がありました。
-
図5 従来基材の縫い目部分での滑脱現象
繊維産業は各工程ごとに会社が分かれているため、新基材開発にご協力いただける原糸メーカー、生地生産会社、樹脂加工会社を探しだし、相談に伺いました。伺った会社は皆、高い技術を有しますが、新しい研究開発には馴染みがなく、最初は新基材開発に対して躊躇されていましたが、何度か打ち合わせをしていくうちに、我々の「マザーシッププロジェクト」実現にかける思いが通じたのか、最終的には新基材開発に承諾いただきました。2021年6月コロナ禍ということもあり、東洋紡株式会社※3(大阪府大阪市)、サカイ産業株式会社※4(静岡県島田市)、東洋クロス株式会社※5(大阪府泉南市)、トヨタ(静岡県裾野市)の4社をWEB会議でつなで決起集会を行い、新基材開発がスタートしました。
チャレンジと課題克服
軽くて耐荷重性の高い基材を作るため、原糸は東洋紡株式会社のトップクラスの軽量高強度のスーパー繊維をベースに、新たに開発いただきました。しかし、この原糸が高温で強度が低下する特性があったため、樹脂加工の際、通常の高温で硬化する樹脂が採用できない問題がありました。それに対し、東洋クロス株式会社が溶剤を用いて低温度でも樹脂が硬化する工程を開発いただきました。さらに繊維と樹脂の密着性を高くするためにスーパー繊維への表面処理もご提案いただきました。
また基材の縫製時の滑脱を防ぐため、生地は織って作ることにしました。織物の生産工程では、途中で糸が切れたり、糸同士が絡まったりしないように、厳重な品質管理をしなければなりません。サカイ産業株式会社が3,000を超える経(たて)糸(織物の長手方向の糸)を一本一本、切れないように手作業で均一に並べるなど、長年の職人技で品質の高い織物を実現してくださいました。
その結果、従来基材に比べ31.5%も軽量された、基材単品の引張強度約1.3倍、縫製部の引張強度が約3倍の新基材が完成しました(図6、図7)。
-
図6 従来基材と新基材との比較。新基材は織物のため密度が均一
-
図7 新基材と従来基材の縫製部の引張強度性能比較。新基材の縫製部の比強度(基材単位質量あたりの強度)は従来基材の約3倍
これから
この新基材でカイトを作り(図8)、2022年3月には福島内陸部※6で24時間連続滞空試験を行う予定です。新基材の使用により、カイトが軽量化でき、縫い目部分の強度が上がったことで、強風に対するカイトの耐久性や飛行安定性も大幅に向上するのではないかと期待しています。
いつの日か「マザーシッププロジェクト」の実現を夢見て、我々の挑戦は続けていきます。
-
図8 新基材使用カイト。著者(板倉)は前列左から3番目
著者:板倉英二
トヨタ自動車が、かつて航空機用エンジンの開発していた際の、型式・製造認証取得の中心メンバー。以降、将来モビリティ企画研究に従事。夢は「マザーシッププロジェクト」を実現させること。マザーシッププロジェクトが防災にも役立てられないか考えています。関心がありましたら是非ご連絡ください。