「もっといい工場づくり」では、トヨタ生産方式に基づいた「1個流し
※」にこだわりながら、「シンプル・スリム」、「汎用化」、「工程短縮」、「明るくきれいで安全な職場」をキーワードに、工場の競争力をより高める取り組みを進めています。開発した新技術は、現在ある量産ラインにも導入することで、既存工場の競争力強化を図っています。
※ 1個流し
部品の生産から組立に至るまで、お客さまのオーダー順につくる生産方式。
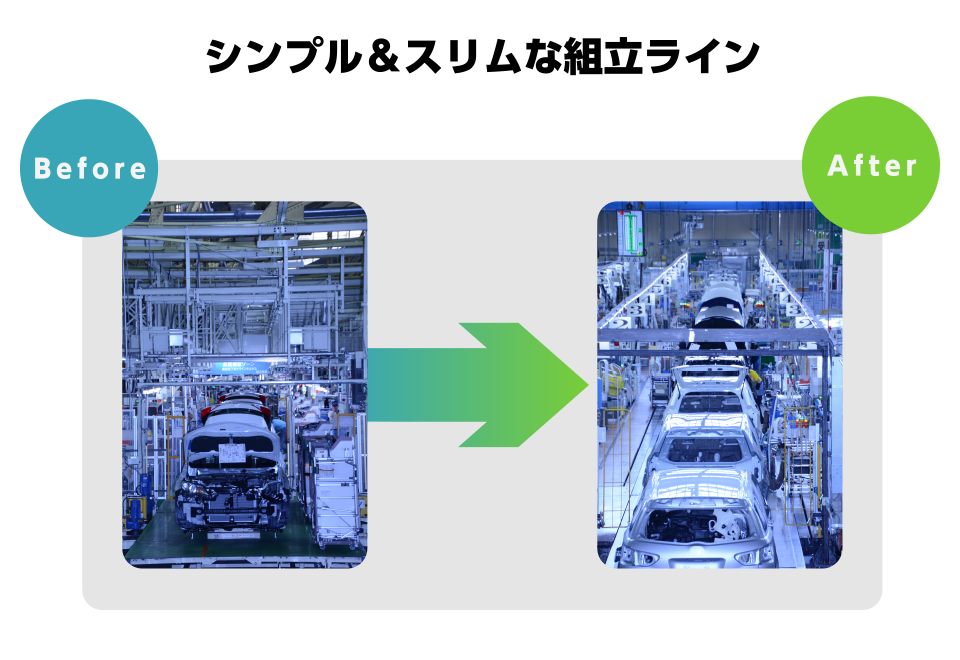
工場の天井から吊ったり、床面を掘るなどして設置していた大型設備を床に直置き可能なコンパクトな設備に切り替えています。
ホットスタンプは、鋼板を加熱して軟質化させてプレス加工し、金型との接触による冷却効果により焼き入れすることで高い強度を実現しています。加熱に電気を用いることで、従来のガス炉に比べて設備を大幅に小型化しました。
ボディの接合には、レーザースクリューウェルディングを使用して新骨格ボディの剛性をさらに高めるとともに、溶接のスピードアップによる工程短縮も可能となりました。
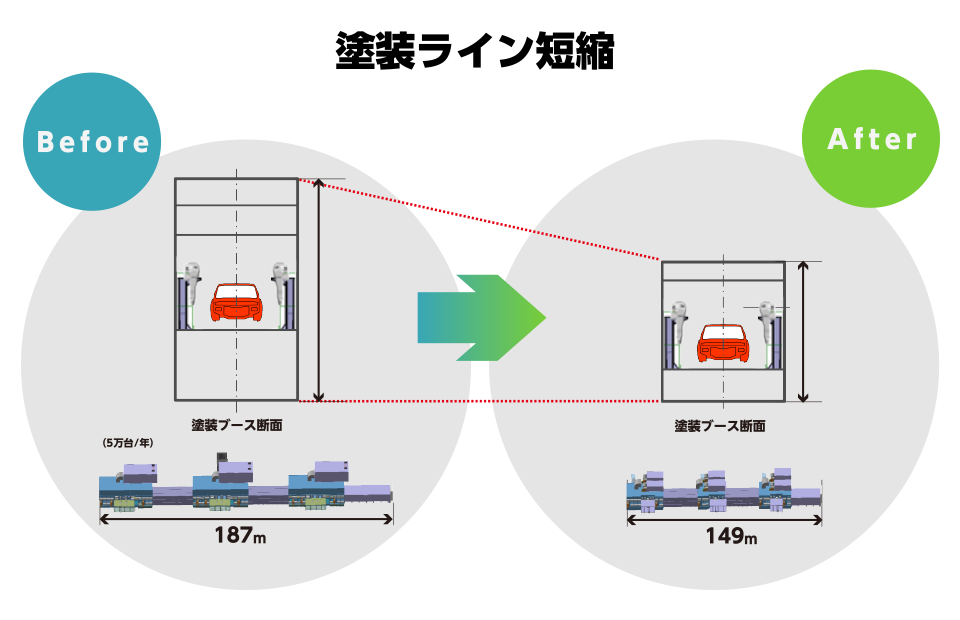
塗装ラインでは、塗装ブースをコンパクト化し、ラインも約187mから約149mに短縮しました。
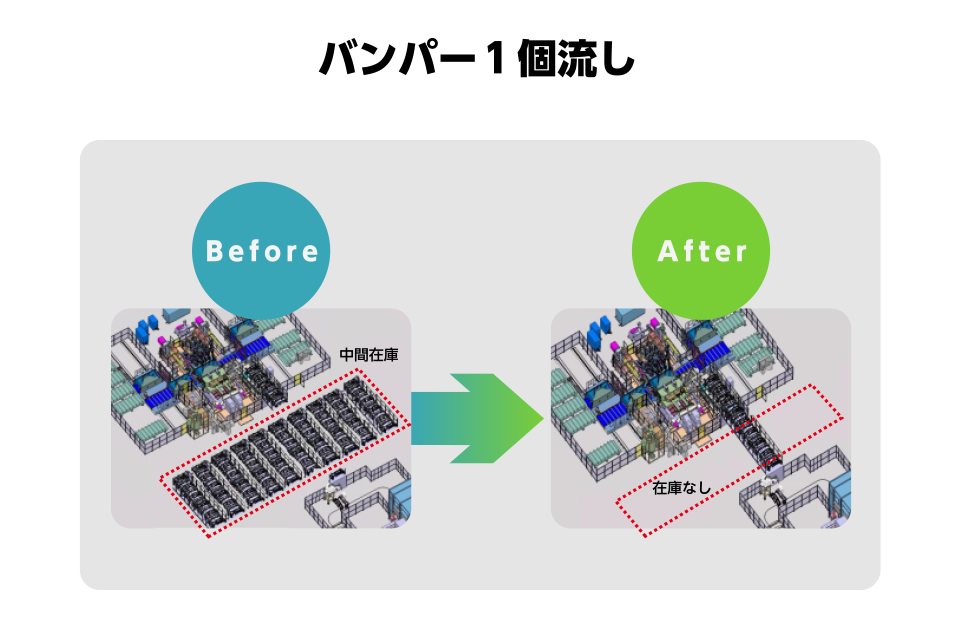
従来、バンパーの射出成形では、塗装工程との間に中間在庫を抱えていましたが、バンパー1個流しを実現して両工程を直結することで、この在庫を根本的になくしました。